Equipped with high performance Panasonic control system, which be able to generate accurate output pulse, and make the instruction cycle more faster and stable. The program is designed to integrate sophisticated function to greatly reduce the time used by operator for data input. Besides, the self protecting program for all actions performed by the machine to avoid the damage.
Using 12 inch WEINVIEW HIM touch screen, and with clear and user friendly software, which boost the data processing and image display.
Panosonic Servo Motor
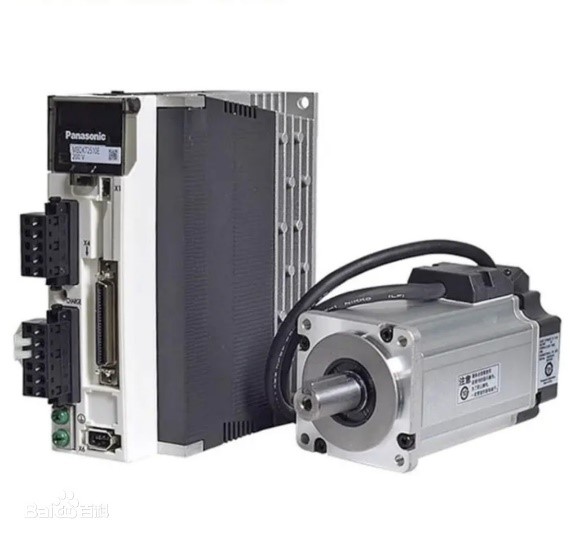
K-series Wound Core Winding Machine equipped with three sets Panasonic servo motors to realize the following actions:
First servo motor: it is for the feeding roller unit, which connect to the reducer and roller, to accurately feed the materials to different position for processing.
Second servo motor: it is for the cutting, which connect to precision reducer, then drive the tungsten carbide cutter to cut materials.
Third servo motor: it is for winding, the belt drive the main shaft, the torque is strong and the positional accuracy is high
Motion Components
Linear guideways: provide a type of linear motion that utilizes re-circulating rolling elements between a profiled rail and a bearing block. The coefficient of friction on a linear guideway is only 1/50 compared to a traditional slide and are able to take loads in all directions. With these features, a linear guideway can achieve high precision and greatly enhanced moving accuracy.
Tungsten Carbide ToolsThe cutting tools is made of the tungsten carbide material with good abrasive resistance, besides, it has good resistance to elevated temperature which improved the cutting speed. The tungsten carbide cutter edge is more sharpper then other cutter, so the sheet is more orderly.
Heat Exchanger
In order to reduce the temperature of the control cabinet, we added the industrial heat exchanger for cooling, which could slow down the aging rate of the electrical components and makes the machine run at the best condition.